今回はキールとラダーのカーボンFRPの積層作業の続きを紹介します。
FRPの積層作業その後
積層作業については
1日経ったので真空を破り型を真空バッグという名の布団圧縮袋から取り出し。
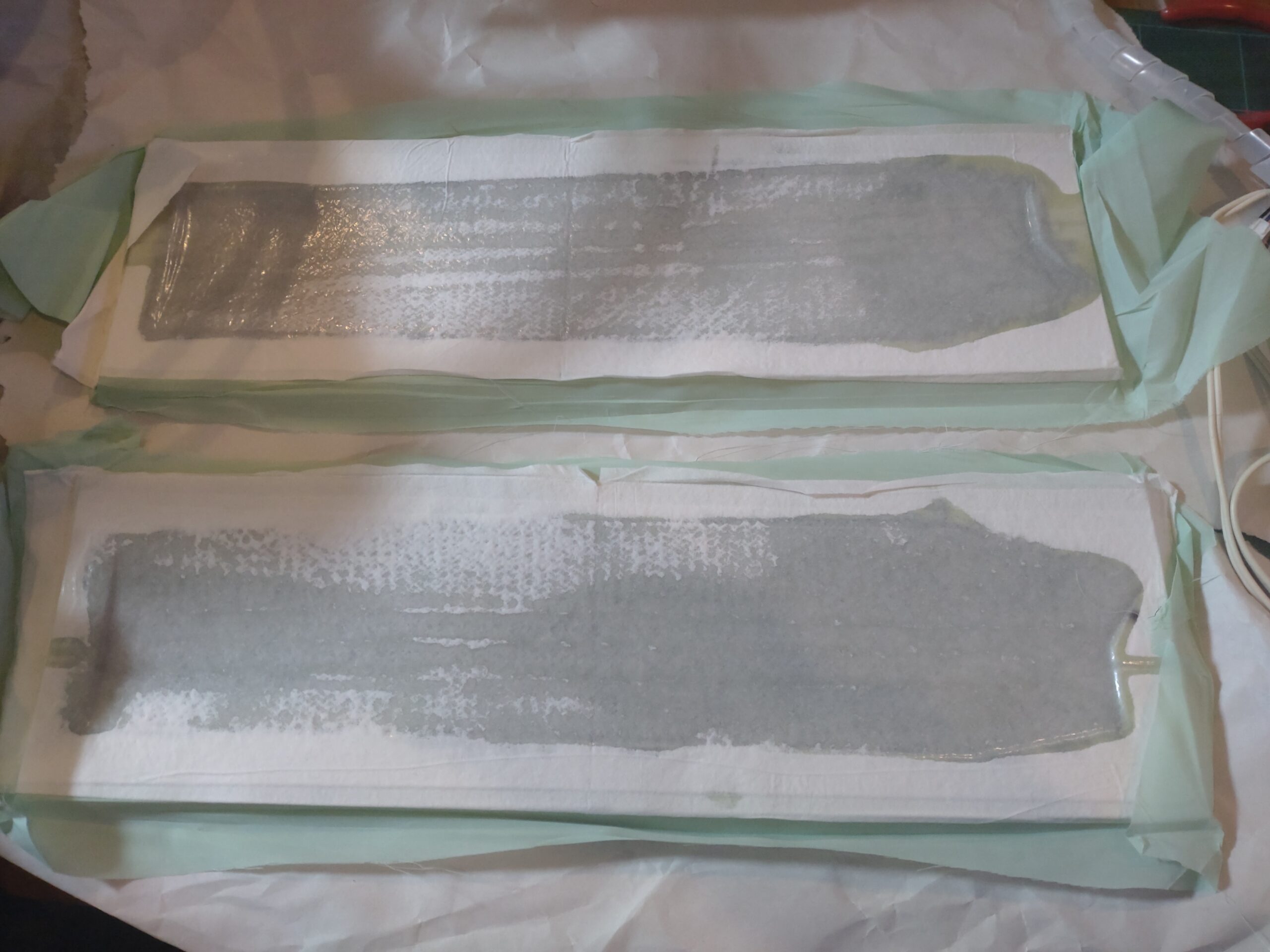
結構樹脂も絞り出されてキッチンペーパーに浸透しています。
脱型
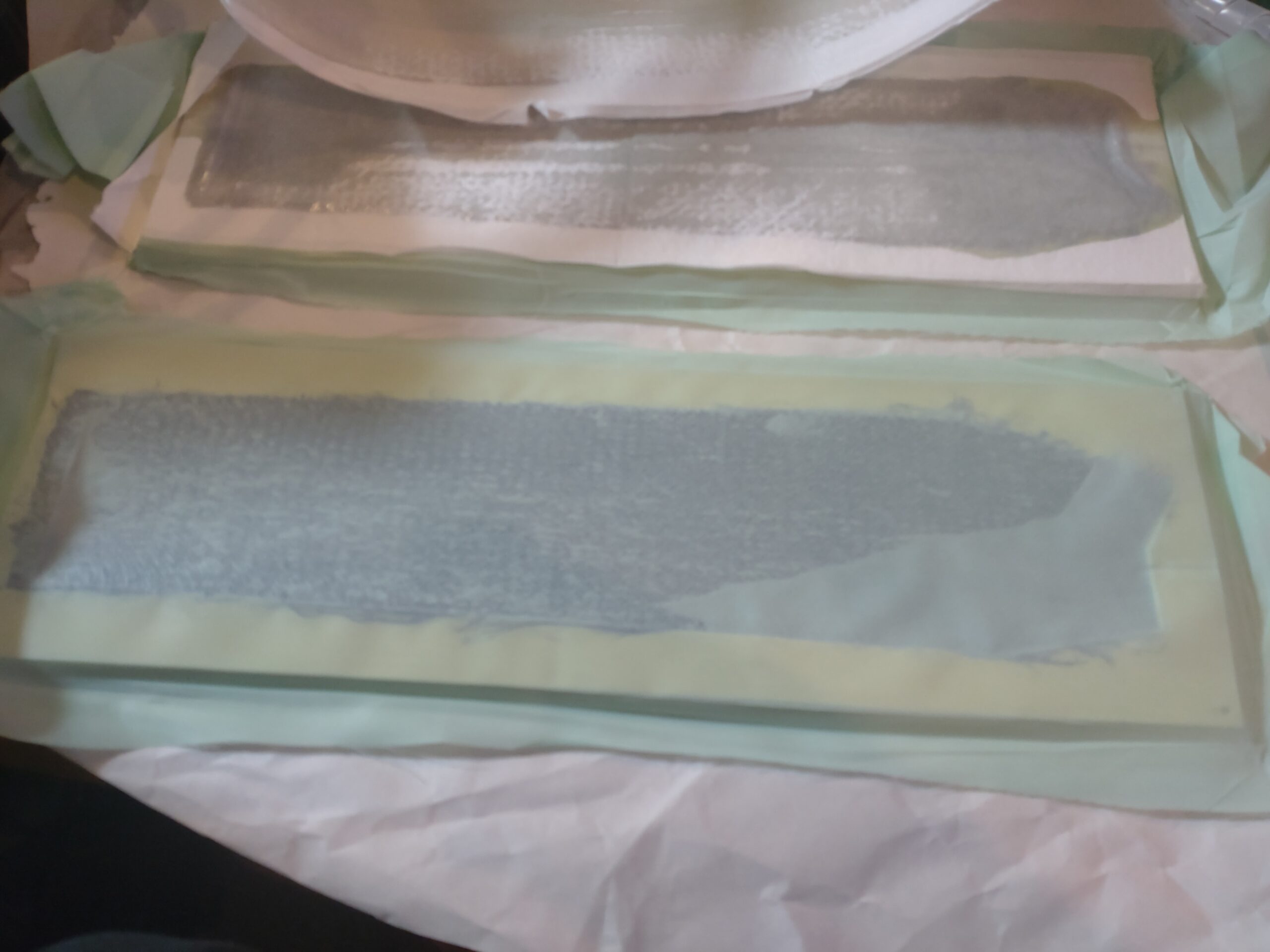
キッチンペーパーを剥がし( ^ω^)・・・。
すでに積層したカーボンがピールプライからいくらか剥がれていますが( ^ω^)・・・。
ピールプライにくっついて積層したカーボンも取れてしまいました。
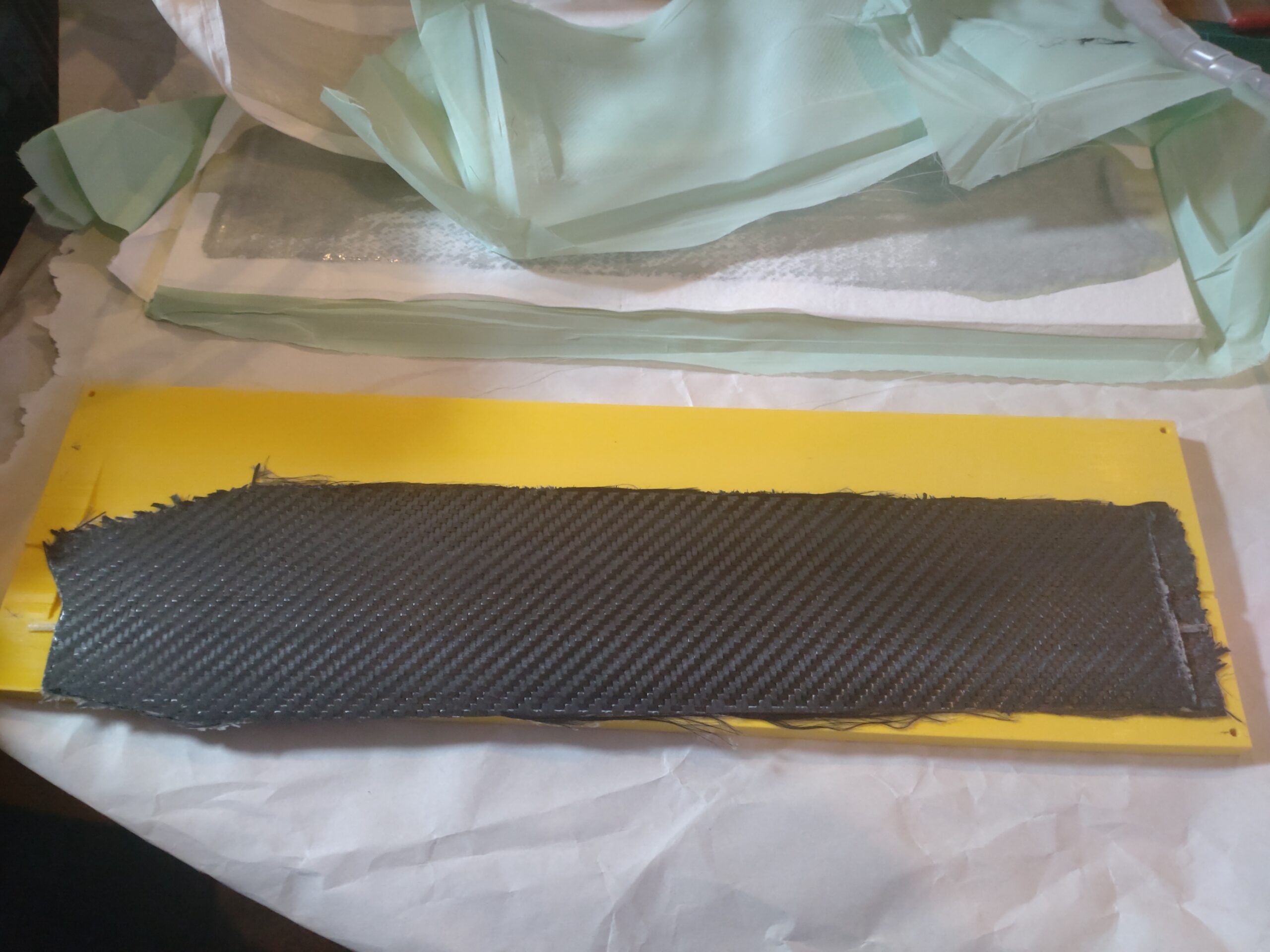
脱型は問題ありませんでした。
ですが・・・。

キールの下端は型に密着してませんでした。
右側は上端も( ^ω^)・・・。
ここは積層していて想定はしていたのでまあ予想通り( ^ω^)・・・。
型の上下に余裕をもって製作するか段差を作らないようにして型を作ったほうがよかったんじゃないかと思います。
上側はキールケースの中に入るんで後で見えなくなる場所なので問題なし。
下側は若干切ってバルブの中に入るのでここも問題なし( ^ω^)・・・。
なんで今回はこのままにします。
積層品の後処理
とりあえず上下と前縁の余分な部分をざっくりはさみで切り取り。
型に積層したカーボンを戻してはみ出ている部分を削り取りました。
キールの後縁については薄くしたいので2層目の45度に傾けたクロスを削り落としました。
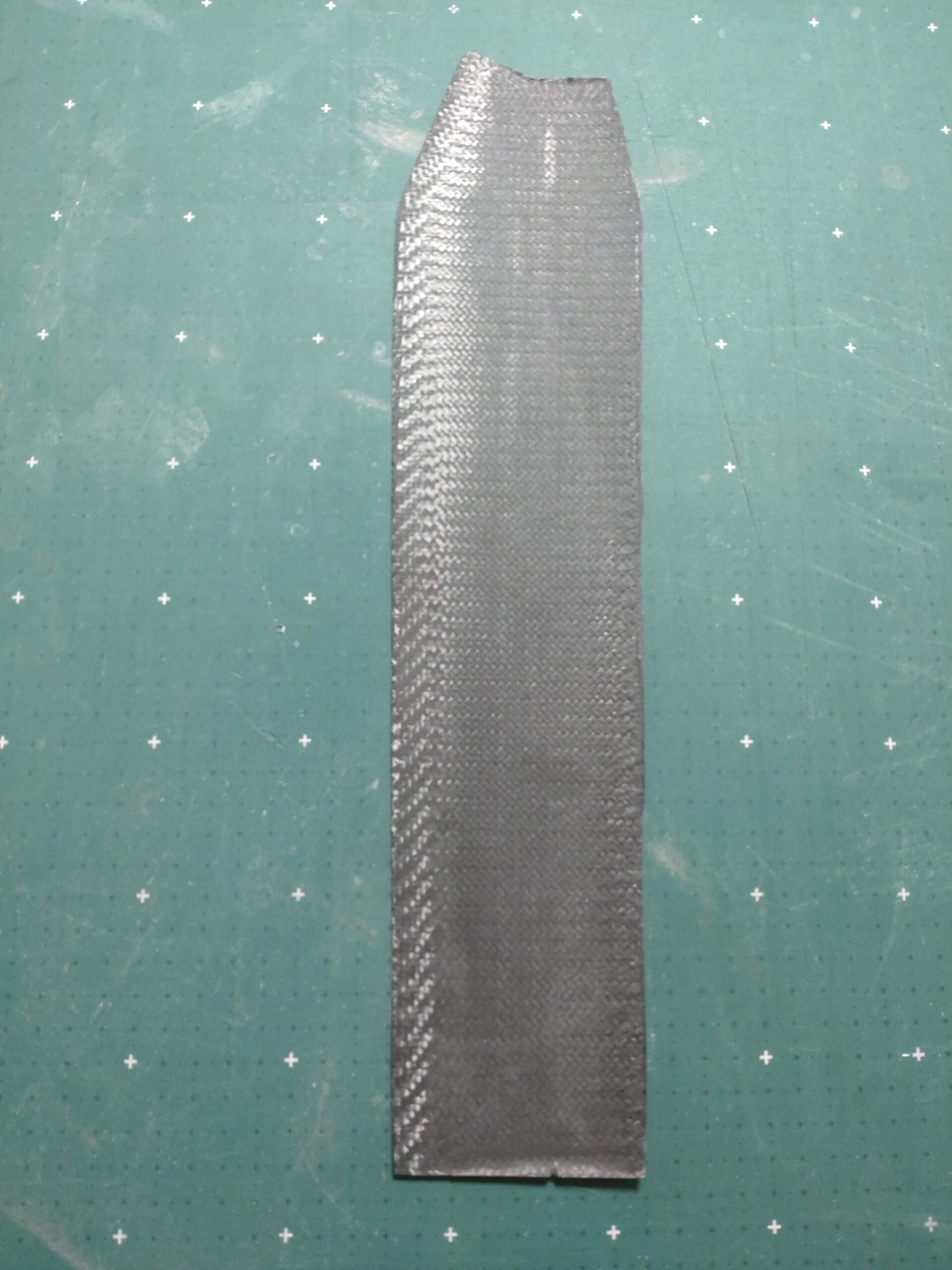
ここは最初から積層しないで作ったほうがよかったのかもしれません。
今回の積層で2プライ部分の厚みは約0.5mmでした。
なので1プライ0.25mmとしてその分の幅を少なくして2プライ目のクロスを小さくカットして積層すれば削り落とす手間が減らせそうです。
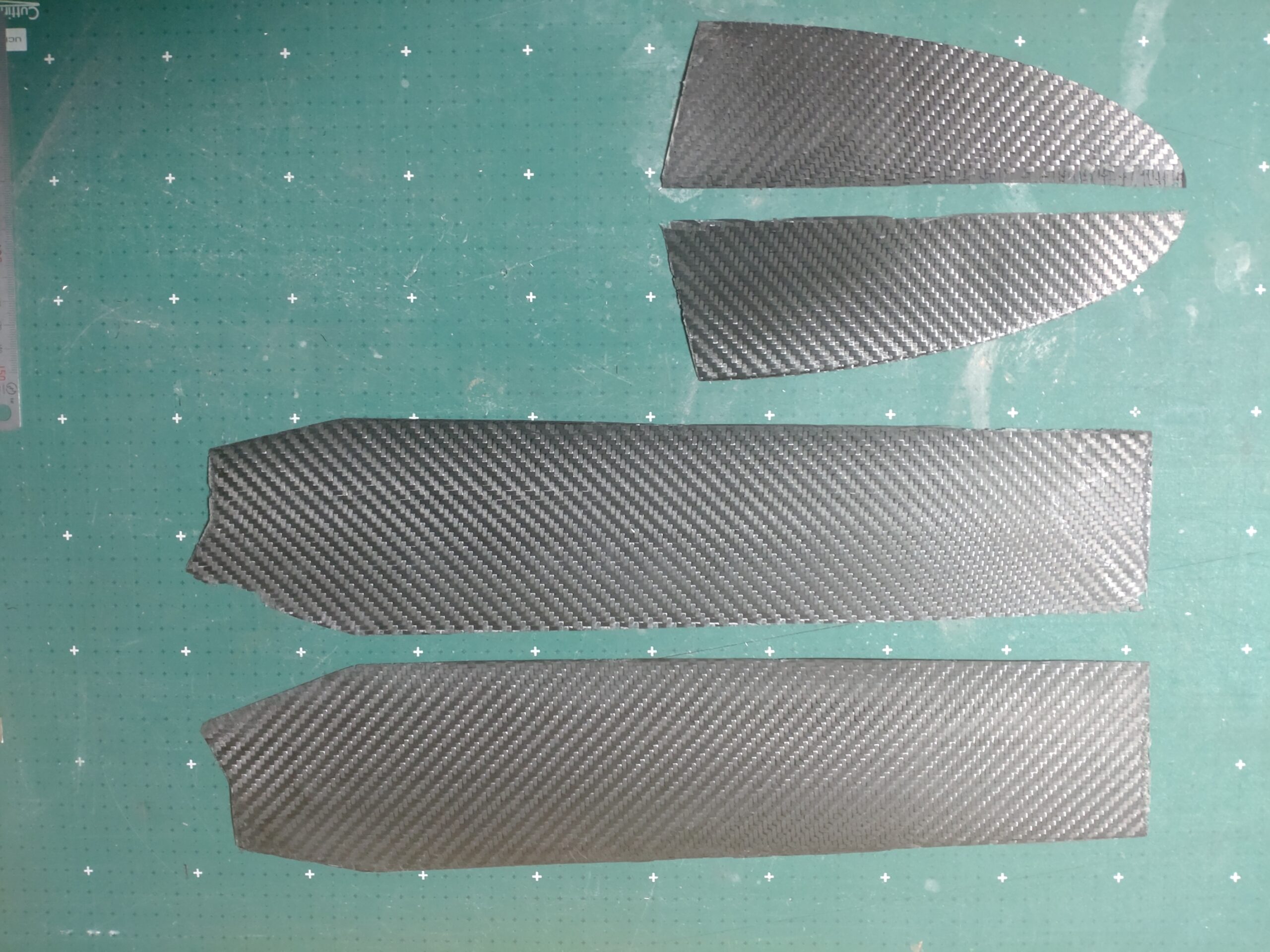
一部後縁は欠損ありますがキールの中に入る部分なんでここもそのままとします。
反省点も多いですがとりあえず無事に積層、脱型が出来ました。
いや~積層物が型から取れなかったり、取ろうとした時に壊してしまったりしてしまうんじゃないかと( ^ω^)・・・。
今回の製作についてはこの作業が一番不安な作業ではあったのですが何とか無事に作業を終えることが出来ました。
記事
R0.0 新規作成 2023.11.12